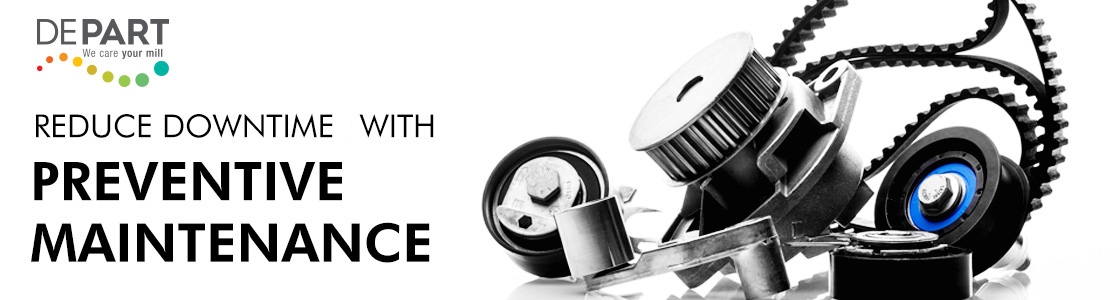
The Positive Impact of Preventive Maintenance on Downtimes
Equipment failures are inevitable. And big problems are often the result of minor problems that were neglected or not noticed in a timely manner. However, by adopting a maintenance strategy that meets the needs of your facility you can ensure that business-critical assets are available at all times.
Unplanned downtimes are among the main problems that challenge production facilities. Downtime is the amount of time for which a system, machine or an equipment is in an inoperable state. These situations which cost significant revenue losses to the world’s top companies every year can be described as any unplanned event that ceases production for any amount of time.
The negative impact of downtimes on businesses is not limited to the disruption in production. The work force allocated to rescheduling, unexpected repair costs, time spent for restoring customer satisfaction and reputational damage are among the other consequences resulting from such events.
Often resulting from operator errors, poor maintenance, software or hardware failures, downtimes are actually not inevitable. Performing regular maintenance on your machinery is one of the most efficient ways of avoiding downtimes.
The two foremost goals of preventive maintenance which can be described as regular and scheduled maintenance are prolonging asset lifetimes and preventing likely failures that may lead to downtimes. Through such a maintenance strategy, it is possible to ensure maximum business efficiency and continuity, as well as operational safety.
However, many manufacturers continue their operations by performing reactive maintenance, that is, the maintenance performed after failures occur since regular and preventive maintenance requires planning. While reactive maintenance is sufficient for certain situations, it causes more frequent downtimes and eliminates the opportunity to prevent small problems from becoming bigger ones.
It is important to have critical spare parts in stock at your plant as part of your preventive maintenance strategy. Otherwise, ceasing production operations while waiting for the spare parts to be procured will result in considerable losses. The investment made for stocking critical spare parts should not be regarded as a financial burden. Spare parts inventory will vary depending on the kind of maintenance activities carried out in specific plants.
A preventive approach that aims to prolog the lifetimes of business assets, equipment and infrastructure through planned cleaning, repair, lubrication, adjustment and replacement increases the availability and operational output of your equipment and machinery. Helping to generate a higher return on investment, preventive maintenance also improves reliability and predictability.
Ideal for assets that are operationally critical, likely to fail with use, subject to legal requirements and have high financial value, preventive maintenance approach can be supported with employee training and smart software systems and technologies.
Depart is a reliable and powerful business partner to respond to all your requests regarding critical spare parts that play a very important operational role in plans of preventive maintenance based on time and use. Offering services such as check-up and expertise work, annual maintenance services, mill capacity increase, process changes and technical training with its expert engineers, Depart aims not only to meet its customers’ spare part requests, but also to resolve their technical issues and reduce their operational costs. You can rely on Depart for all your maintenance and spare parts needs.