The Significance of Pneumatic Cylinders and Equipment in the Milling Industry
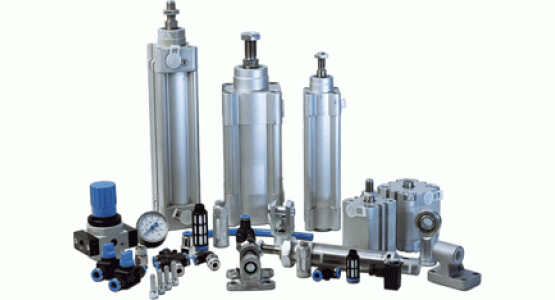
Categorized under the pneumatic group, pneumatic cylinders and equipment play a critical role in the milling industry. Used in different points and machines in mills, these cylinders and equipment significantly affect the efficiency of milling operations.
Pneumatic cylinders use the force of compressed air to generate a linear force. Therefore, they are also known as compressed air cylinders. These products enable a high level of cost-effectiveness for a broad application range even under the most challenging conditions. They are also very simply installed. Pneumatic cylinders are robust and flexible epuipment, highly resistant to the effects of high external forces.
With their durable aluminum bodies and long operating lives, pneumatic cylinders offer significant advantages to millers. Used in automation technology and factory automation, pneumatic cylinders are typically preferred in applications such as tensioning, lifting, countersinking, pushing, pulling, feeding, turning, gripping, clamping and holding, joining, and stopping.
A pneumatic cylinder moves the cylinder piston in a specific direction, using the power of compressed air. The piston’s motion is transmitted to the parts to be moved via the piston rod. They are operated with compressed air of up to a maximum of 12 bars to generate a linear or rotary motion.
There are two types of pneumatic cylinders: single-acting and double-acting. Single-acting pneumatic cylinders have only one compressed air connection. The incoming compressed air moves the piston in a specific direction and that is where the cylinder force builds up. When the piston needs to return to its initial position, the air is expelled from the cylinders and the mechanic spring pushes it back to its former position. They are also equipped with a ventilation hole to prevent the generation of excess or low pressure through the piston movement in the second chamber.
Offering the advantage of a defined position in the event of a power failure, single-acting pneumatic cylinders help reduce air consumption. On the other hand, the stroke length is limited as it is spring-dependent. For the same reason, the force builds up in one direction and does not allow constant force.
Double-acting pneumatic cylinders require compressed air for every movement direction. In these pneumatic cylinders, both the advancing and retracting direction is built up using compressed air. Although they offer the advantage of constant power, double-acting pneumatic cylinders have no defined position in the event of power failure. However, their stroke length can go up to several meters.
The choice of pneumatic cylinders and equipment should be based on the specific conditions and needs of milling operations. As every milling plant has its specific requirements, the ideal pneumatic cylinder would vary from one plant to another. Among the factors to be considered are the working and ambient conditions in the mill, as well as the materials used.
Choosing the right pneumatic cylinder is important for efficiency and operating life. When making this choice, millers should consider the suitability of cylinder arrangement (single-acting / double-acting), cylinder type (compact / guided), force output, and cylinder speed and air consumption with existing conditions.
As Depart, we offer sales, marketing, and aftersales services in over 80 countries. Our range of pneumatic cylinders and equipment contributes to the milling, separation, rice, wheat processes, pasta, conveyor, and packaging industries. With our teams of experienced experts, we provide extensive support in choosing the right equipment and devices, helping millers achieve maximum efficiency in their operations.
If you wish to improve the efficiency and quality of your milling operations, you can contact our sales representatives to learn about our durable, high-quality, and long-lasting pneumatic cylinders and equipment. Regardless of where you are across the world, Regardless of your mill’s location, you can smoothly meet any spare part needs you may have via our e-commerce platform Depart Shop (shop.departspares.com), available 24/7.