The Use and Importance of Elevator Buckets in Flour Milling
The performance of elevator buckets, which enable products to be transported and transferred between different sections in mills, is among the determining factors in both the operation and efficiency of the elevator system.
In the agricultural sector and many other industries, elevator buckets are used to transport bulk materials to targeted locations. Mounted on elevator belts or chains, an elevator bucket takes materials from a loading point and carries them to a certain height before leaving them at a discharge point.
Similar to conveyor belts, elevators differ most from conveyor belts by utilizing buckets attached to a rotating belt or chain to move materials like flour or grain. For the collection and transportation of powder or granular materials, elevator buckets provide the necessary containers bolted to vertical conveyor belts for lifting and holding. It ensures that the material is taken, transported to the desired endpoint, discharged, and returns to the starting point to receive a new load at the final stage.
A mill’s elevator buckets are crucial to the healthy operation of the elevator system, and therefore to the efficient operation of the mill. For this, the product carried must not leak and the system must provide the desired capacity with minimal energy consumption in the targeted period. At this point, a well-designed elevator and correctly selected elevator buckets are the basic factors in the successful operation of the elevator system.
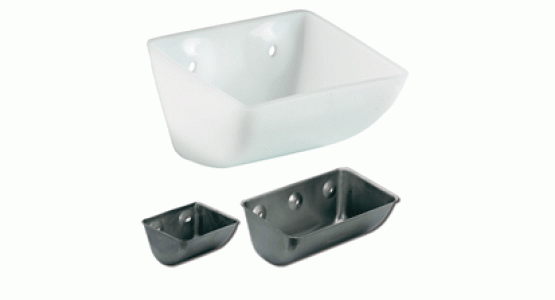
Choosing the right elevator bucket
Selecting the elevator bucket that will provide the best results in transportation operations is affected by a number of factors. For example, the type of material to be transported, the characteristics of the equipment and the elevator system directly determine the performance of the elevator bucket. It is important to take into account restrictions such as the density, humidity, particle size and temperature of the material to be transported.
The service life of an elevator bucket varies depending on the material it is manufactured from and the production conditions, as well as the characteristics of the product it carries. Elevator buckets, which are generally used to transport raw materials in flour, animal feed, pasta production, cement industry and recycling facilities, are made of metals such as aluminum, cast iron, plastic or steel depending on the type of product being transported. For example, when transporting highly abrasive products, plastic elevator buckets with high resistance to abrasion should be preferred. On the other hand, elevator buckets made of specially compounded materials are used when transporting wetter and stickier materials, such as molasses. In the flour and grain industry, plastic or steel buckets are mostly used depending on the type of product to be transported.
Features of Plastic and Steel Elevator Buckets:
Plastic Elevator Buckets:
- They are resistant to abrasion.
- They do not get damaged because they flex when they encounter an obstacle during the transport process and then return to their original shape.
- Since a lighter elevator belt can be used, they have weight savings that can reduce energy costs. In this way, it also extends the service life of other drive components.
- Lightweight plastic buckets with low profile cuts can be placed closer to each other, thus increasing capacity.
- No risk of sparks if friction or collision occurs during operation.
- Polyethylene and polyurethane are FDA approved for use in food applications in the United States.
Nylon, polyethylene and polyurethane buckets often offer a significantly more economical option up front
Steel Elevator Buckets:
- They are durable and long-lasting.
- They can withstand the rigors of heavy-duty operations, reducing replacement frequency and associated downtime.
- They can be customized to specific requirements, including size, shape and capacity. This flexibility provides options that provide optimum performance in a variety of applications.
- They are suitable for high-temperature materials, providing safer performance in operations involving heat.
- They can be prone to rust and corrosion, especially in humid or wet environments, if not properly maintained.
- They are generally heavier than plastic buckets, which can increase the overall weight of the elevator system and require more energy.
- Initial investment may be higher than plastic options.
- Steel buckets can be crushed during operation, resulting in loss of capacity; friction can increase the risk of sparks.
Explore the high-performance elevator buckets from Depart!
Depart offers elevator buckets that are break-resistant, flexible, suitable for variable temperatures and resistant to abrasion for mills.
Depending on your mill’s needs, our steel or plastic elevator buckets work effectively in a wide range of speeds. For more information about Depart’s stainless steel elevator buckets (pressed/seamless) or plastic elevator buckets (nylon, HDP or polyurethane), please contact us: info@departspares.com
Visit our secure online shopping platform Depart Shop to view and purchase different elevator bucket options.
Sources:
https://millermagazine.com/blog/use-of-elevator-buckets-in-flour-and-feed-milling-industry-and-its-importance-3493#:~:text=Elevator%20buckets%20are%20containers%20for,hold%20and%20lift%20the%20material.
https://www.linkedin.com/pulse/use-elevator-buckets-milling-industry-its-importance-samarth-gupta
https://rosal-feedmills.com/en/machinery/conveying/bucket-elevator/#